In this article we talk to EUR ING Professor Darren Williams MEng, EngD, CEng FIET, MWeldI, who works for TWI Ltd as Welding Systems Team Manager and for Lancaster University as Director of the Joining 4.0 Innovation Centre (J4IC), a strategic partnership between TWI and Lancaster University. Both roles focus on research and development (R&D) of novel, digital technologies for implementation in welding and joining techniques.
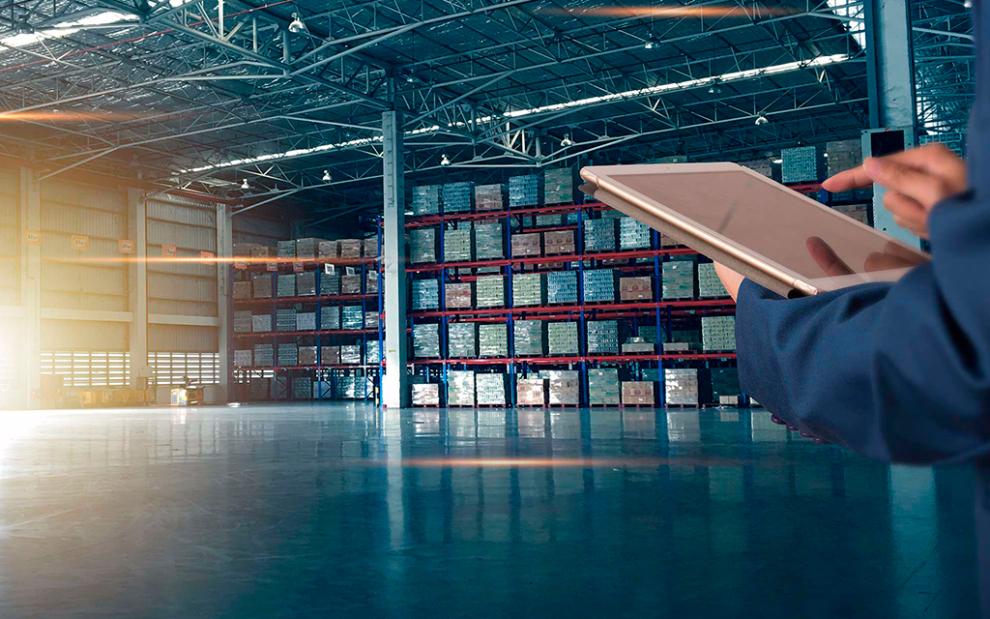
The Up-Skill project: Up-skilling for Industry 5.0 Roll-out project, is focused on building a better understanding of how businesses in industrial and manufacturing environments can leverage value from human-machine integration. In particular, Up-Skill is looking at what happens when new, ‘intelligent’ production technologies are introduced into organisations, examining how artificial intelligence (AI), robotics and other technologies can change working practices, the skills people use, and how they respond to and interpret the practices. Research undertaken during the project will also map out wider changes that could occur, using ethnographic studies to consider working methodologies and social interactions, and routes to understanding and obtaining the technologies to be implemented.
Prior to joining TWI, Darren worked for Rolls-Royce where he played an integral part in setting up a brand new, state-of-the-art production facility, the Advanced Blade Casting Facility (ABCF). While there, Darren was the Area Process Owner, responsible for optimising and managing automated production lines, product integrity, training and continuous improvement as well as leading engineering teams.
Darren has been an active volunteer for over 19 years, receiving national recognition for his contributions including:
- Paul Fletcher Award 2019 Winner – The Institute of Engineering Technology (awarded annually to an IET volunteer for outstanding achievement in contributing to the Institute’s activities)
- 2018 British Black Business Award (BBBA) Winner – Science Technology Engineering Maths: Rising Star, STEM category, under 35 years old (BBBA is a premium awards programme, receiving 1000’s of entries each year, that recognises, rewards and celebrates, exceptional performance and outstanding achievements of black people in businesses operating in Great Britain)
- 2017 STEM Ambassador of the Year 2017 – awarded by the prestigious Armourers & Brasiers in recognition of volunteering activities contributing to the promotion of engineering
Darren was appointed Director of J4IC in 2020 and, since then, has established the Centre as a key digital partner focused on artificial intelligence (AI), machine learning, and the connection and enhancing of legacy systems within a welding and joining context. Find out more about some of J4IC’s projects.
In this interview with Darren, we take an insightful look at the Up-Skill project, which J4IC is a consortium partner on.
Why did J4IC join the Up-Skill project?
The Up-Skill project aims not only to identify the key features of the topology that defines human-machine relations in industry 5.0 but to define the managerial competencies needed to succeed in this space. Up-Skill will link different strategic contexts, technology implementation and detailed workplace ethnographies within a single research project, primarily addressing the workforce implications of industry 5.0, in the context of the relationship between automation choices and maintenance of skilled work. J4IC, therefore, joined the project to support the ethnographic studies based at end user organisations, and develop and apply AI and machine learning across these use cases.
How are human-automation challenges related to the core values of Industry 5.0 and expectations of the EU?
To me, the real challenges of industry 5.0 are similar to those of Industry 4.0. The personal dynamics of an organisation can, in an ideal world, be the greatest assets and drivers for innovative change. However, more often than not, they are the inhibitors of change. There is no employee/employer differential here, as resistance can often be observed across the organisation’s structure. Therefore, creation of a transparent organisational structure, with strategic aims that are fully visible to all, could go a long way towards mitigating the inherent mistrust which hinders innovation and technological change. Artisans are the very lifeblood of these SMEs but they are a dying breed. Young school leavers are not drawn to manual careers which are perceived to not have a wider market worth. The demise of the craft apprenticeship has only exacerbated the problem and now these artisanal SMEs are witnessing an aging workforce. The replacement of skilled artisans with technologies can only go so far and runs the very real risk of devaluing the product in the consumer’s perception. This, therefore, would be self-defeating. Two of the use cases the consortium is working on represent the extremes of industry 5.0: one is a large company embracing digitalisation but finding it challenging to convince the workforce of the benefits of some aspects, while the other company is small and artisanal, and wishes to introduce some new technology to reduce production costs.
How is J4IC’s research experience informing its work on Up-Skill?
Darren tells us that J4IC has two skilled engineers working on Up-skill, Peter Wilson and Andrew Gridley, who between them have decades of engineering experience in manufacturing research and production.
We asked Peter, a Post-Doctoral Research Associate, about his career to date and his experience of working on the Up-Skill project, to which he responded “Thirty years in industrial R&D has informed my view of the ever-present issues preventing innovation and growth. Positively, Up-Skill has highlighted and addressed some of these through the delivery of the project.” Adding “J4IC’s role and work on the project has encompassed developing CNC, robotics and software applications, incorporating AI into visual inspection systems, automating brazing techniques and proposing design alternations, and more.”
How is Up-Skill contributing to the transition companies will be required to make while simultaneously keeping intact the core values of Industry 5.0?
As AI technology is currently here and available, I am of the belief that we can use the tools effectively to enhance the workforce and increase productivity. Up-skill has showcased various industries, which have had a number of technological and personal challenges when adopting innovative technology. For example, if an industry struggles to retain skilled workers or is facing an aging workforce, then technology can be used to capture artisanal approaches and make an automated solution – creating new skills within the workforce while maintaining productivity.
What benefits do you hope J4IC’s participation in Up-Skill will bring to the project?
My hope is that the industrial partners will see a true benefit from the technological advances being made through the project, and that these will improve and enhance the skilled workers’ professional experiences. On a wider note, I would hope that: the artisan’s work and skillset within industry and society at large can be better valued; the potential stigma of choosing a manual craft career removed; young people can envisage a career that is rewarding without holding a university degree; and we may see a rejuvenated apprenticeship system in the future.