A new report, led by Anglia Ruskin University, provides a detailed examination of the implementation of digital technologies across various manufacturing firms. The report synthesises lessons learned from multiple case studies, highlighting the complexities and challenges faced by organisations in adopting new technologies.
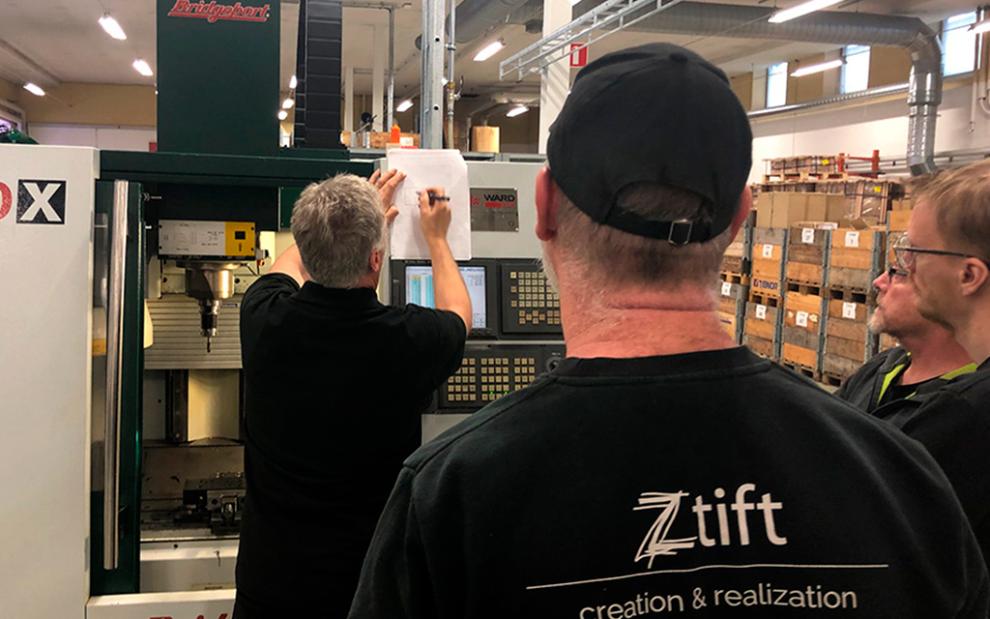
The report begins by discussing the organisational contexts in which new technologies are introduced.Contrary to the pristine, high-tech images often associated with Industry 5.0, the reality is a mix of old and new machinery, human skills, and established work practices.This "mixed ecology" creates a unique environment where new technologies must coexist with traditional methods. For instance, one company retains old machines due to their reliability, while another integrates new technology into a cramped workspace filled with personal and professional artifacts.
Motivations for Implementing Technology
A significant driver for adopting digital technologies is the intention to reduce labour costs and human error. Some firms aim to replace manual tasks with automated systems to improve efficiency and accuracy.However, this approach is not without its challenges. For example, one company faced difficulties in replacing a skilled metalworker with a combination of machines, highlighting the limitations of automation in replicating human dexterity and expertise.
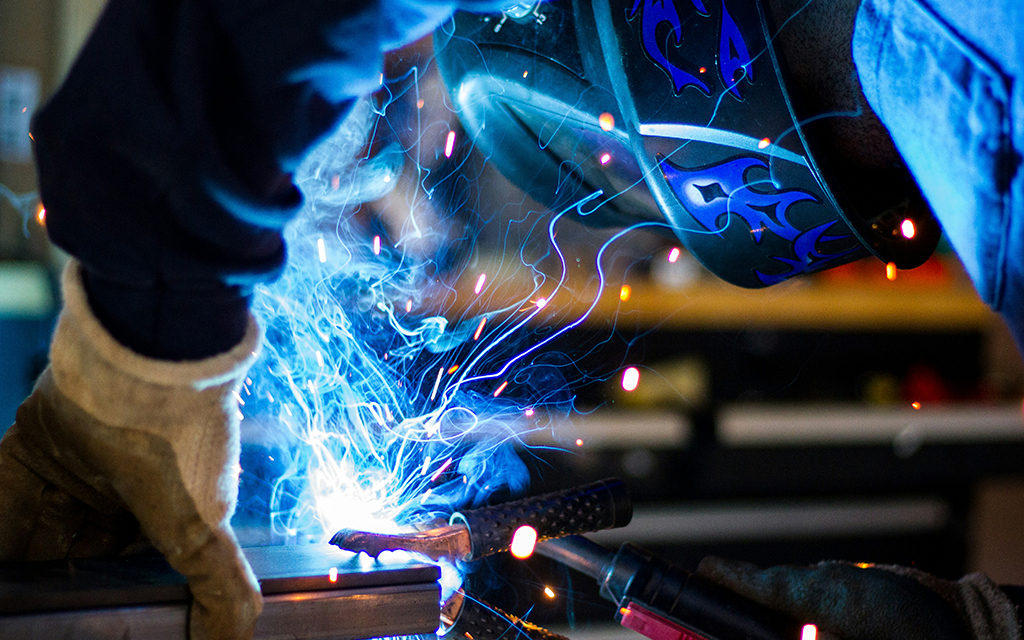
Another motivation for adopting digital technologies is the desire to obtain accurate, real-time production data.Manufacturing Execution Systems (MES) are commonly used to track production processes and identify bottlenecks. However, the implementation of these systems can also serve a disciplinary function, as seen in one firm where workers' output is closely monitored. This dual purpose of MES highlights the tension between improving efficiency and maintaining a positive work environment.
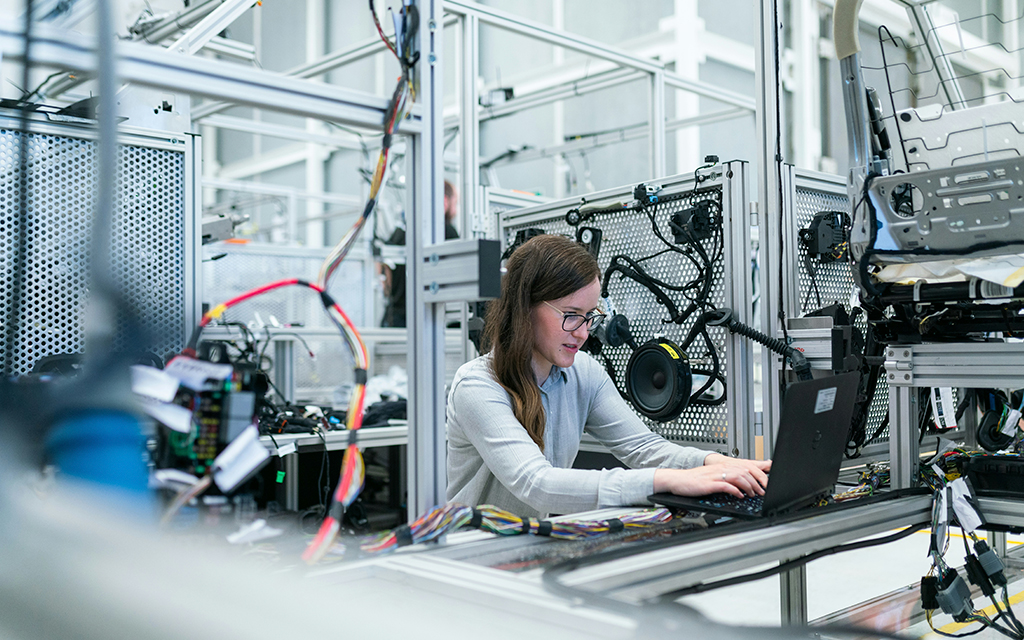
However, it has been observed that small companies often face significant challenges in recruiting staff, particularly for skilled manufacturing jobs, and it is the scarcity of human skills that appears to be the primary driver for seeking technological solutions.For example, one company recognises skill scarcity as a crucial factor for automation, valuing their workers' ideas and contributions while introducing machines where skills have been lost.Similarly, another company successfully employed a CNC system operator using traditional job posting channels, but faced difficulties in recruiting for other roles, leading them to rely on informal networks and personal recommendations.
And this is not an isolated case. For roles involving traditional manufacturing skills conventional recruitment methods have can have limited success.Some companies have hired workers through formal, certificated routes, but others struggle to attract talented apprentices. This has led to a shift towards informal recruitment channels, seeking individuals with the right attitude rather than directly relevant skills. For instance, one company hired individuals from diverse backgrounds, such as nursing and hairdressing, based on their willingness to learn and their commitment to the job.
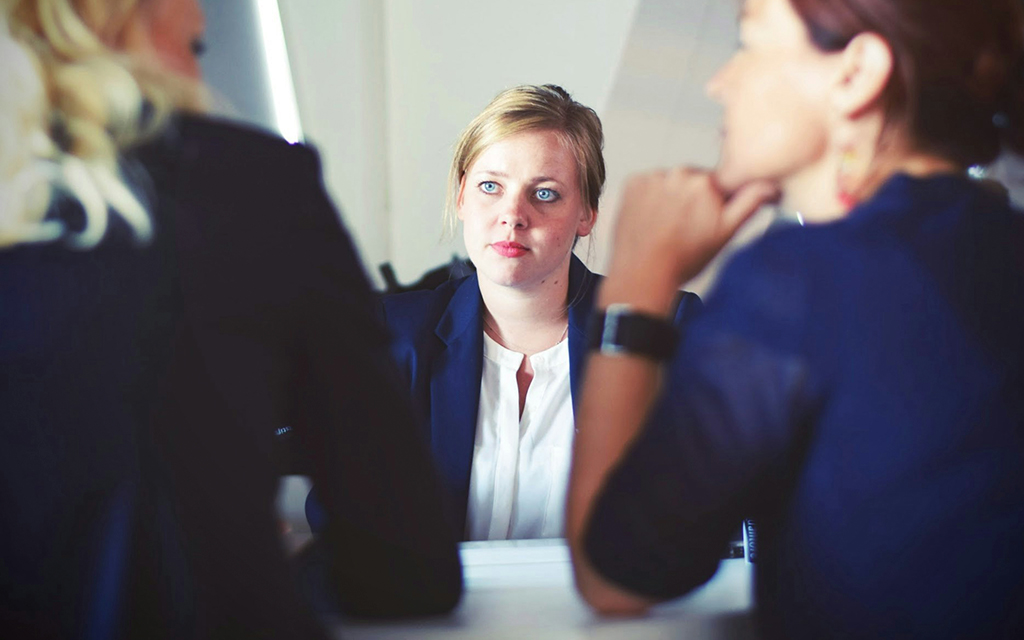
"Craft Attitude"
The implementation of new technologies varies widely among firms.Some adopt a "big bang" approach, introducing new systems without prior consultation with employees, while others involve workers in the decision-making process. The latter approach is generally more successful in ensuring technology acceptance and integration.For example, one firm used an iterative process of trial and error to develop a new production system, engaging workers in testing and refining the system's functionalities.
Related to this, the report emphasises the role of workers' curiosity and expertise in driving innovation. In several cases, employees' interest in experimenting with new technologies led to significant process improvements. This "craft attitude," characterised by dedication to the product and a willingness to explore new methods, is a valuable asset in the digital transformation of manufacturing. For instance, one company's employees embraced 3D printing, integrating it into their workflow and enhancing their capabilities.
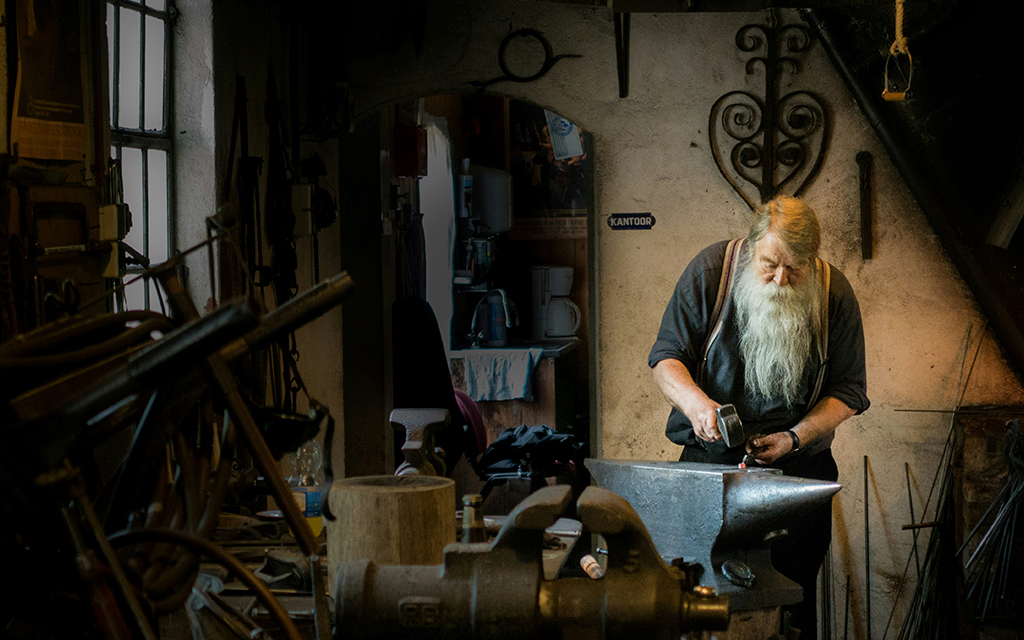
"Craft attitude" has been regularly observed in several small companies and, surprisingly, in larger manufacturing companies characterised by employees taking extraordinary care and meticulousness in their work. At one company, a highly skilled craftsman known as the "Picasso of Mechanics" exemplifies this attitude by making the inside of products as clean and beautiful as possible, even if it may never be seen again.Similarly, at another company, great emphasis is placed on tidy cabling of switch boxes, even in places only visible during maintenance, reflecting a commitment to high standards.
This craft attitude extends to the care and responsibility workers show for their machines and workspaces. It was observed that operators take great care over their part of the production process to provide a perfected part-completed product for the next person in the workflow.This involves highly skilled, embodied practices for operating and managing machinery with precision. The strong ownership, responsibility, and care for individual machines and workspaces, combined with respect for the work done in previous operations, highlights the craft attitude's significance in these companies.
Motivations for implementing technology in small companies and manufacturing environments are often driven by the need to address skill shortages and the desire to maintain high standards of craftsmanship.The “craft attitude” observed in these companies will help researchers better understand what the “human-centric” implementation of advanced digital and automated technologies could look like and help ensure that new technologies are integrated in ways that enhance quality, respect tradition, and leverage human skills. It may also help foster the human-centric, innovative, and collaborative approach to technology adoption, which is essential for the successful implementation and long-term sustainability of new systems in small companies and is the core of the Industry 5.0 paradigm.
Summary
Overall, the report underscores the importance of considering the human and organisational context when introducing new technologies. Whilst digitalisation and automation offer significant potential benefits, its success largely depends on management´s understanding and attitude towards the economic, social and technical impact of technology implementation and, as a result, how carefully these new systems are integrated with existing practices and the active involvement of workers. The findings suggest that a balanced approach, combining technological innovation with respect for traditional skills and practices, is essential for the successful roll-out of Industry 5.0.